News -
Innovation From the Factory Floor: Yamaha Motor’s SpinForged Wheels Yamaha Motor Newsletter(Nov. 11, 2021 No. 93)
Developed for the all-new 2021 MT-09 motorcycle, Yamaha’s SpinForged Wheels established a new and innovative way to reduce weight through the flow forming process they are manufactured with. One of the key drivers that led to the successful application of this method with a mass-production motorcycle for the first time in the world was the development of a special aluminum alloy tailored specifically for flow forming by Yamaha’s in-house materials research departments. In this issue, we introduce the aluminum specialist at Yamaha who played a central role in the development process for creating these new lightweight wheels and some of the challenges she faced.
Harnessing the Talent of an Aluminum Research Specialist
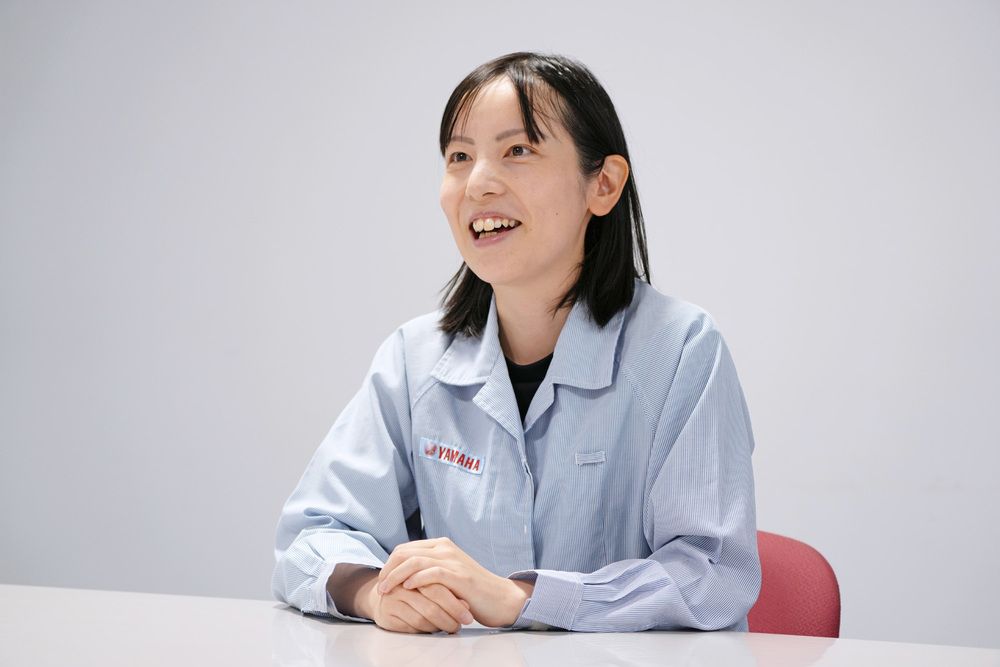
“Just changing a few conditions can completely alter how aluminum reacts, or its ‘personality’ so to speak,” says Kahori Oshima of Yamaha Motor’s Materials Division. She speaks of the metal as if gleefully introducing a friend or close acquaintance. “It can be really sensitive sometimes, often giving us zero margin for adjustments.” Despite this “personality,” aluminum is an essential material used to create our motorcycles, outboard motors, and various other Yamaha products.
Since joining the company, Oshima has worked as a materials researcher specializing in aluminum and her work and findings have won her praise and trust from Yamaha’s development and manufacturing arms. “She’s a passionate and skilled artisan of aluminum and her findings are something Yamaha is very proud of,” proclaims her superior.
Further, while the material itself may be spoken of as simply “aluminum,” what is required of the material can greatly differ depending on the product in question, where a part is to be used, and the machining method called for. “Yamaha has a massive collection of aluminum ‘recipes’ created by our predecessors and this is one of our strengths,” continues Oshima. “We have an ethos here of aluminum being an area of manufacturing that we must never be outclassed in, and I think what lies behind that is the fact that Yamaha has long done casting all on our own. That confidence and pride pushes us.“
Working with aluminum entails carefully controlling the temperature of the red-hot molten metal, mixing the secret blend of additional elements in, and then heat-treating the formed piece to finish it. Oshima’s task as a researcher is to call on her academic knowledge as well as apply new ideas to find the right balance of stiffness and flex while pursuing not only excellent overall strength and toughness but also beauty.
Innovations Born on the Factory Floor
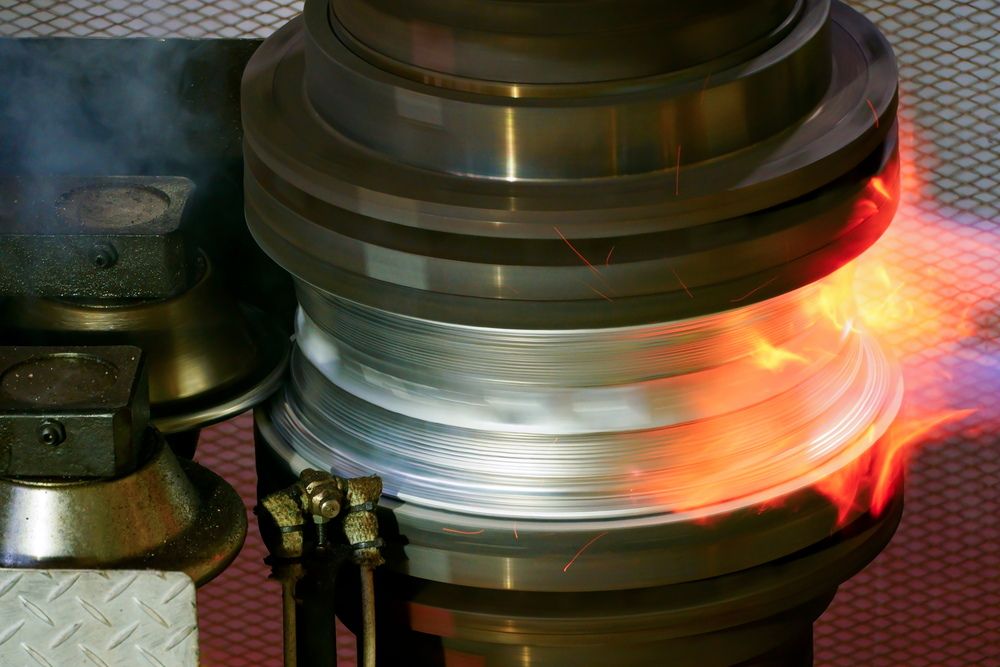
The new aluminum wheels fitted to the latest MT-09 are machined using flow forming and are a standout manifestation of Oshima’s research.
In developing this model, Yamaha embarked on a new and ambitious challenge of extreme weight reduction, driven by the idea that if you can somehow augment the base characteristics of the aluminum, it will spur new innovations to come from the factory floor itself. The engineering and manufacturing departments both threw themselves into the project and successfully created a special aluminum alloy and heat treatment process even their predecessors had yet to concoct. This combination enabled the company to offer the first mass-produced flow-formed motorcycle wheels. Naming them Yamaha SpinForged Wheels, each boasts rims just 2 mm thick (compared to 3.5 mm with the outgoing model) and the front and rear wheels together are some 0.7 kg lighter. Weight reduction is among the most challenging tasks in the industry and such a success makes these wheels worthy of being hailed as innovative.
“What we struggled with the most was having no metrics to go on. Without them for evaluation, we can’t figure out where we need to set our target, so it was certainly difficult to develop a material and build an appropriate method of evaluation at the same time,” confesses Oshima. However, the struggle and hard work made the achievement that much more rewarding and she has immense pride in these wheels.
“For example, if it’s strength alone, aluminum can’t beat iron. But on the other hand, aluminum has advantages like its lightness, corrosion resistance, high machinability, and its beauty. Even if our Monozukuri changes in the future, I’m certain aluminum will remain a material of choice. I believe my role as a materials researcher is to extract and enhance that potential.”
Yamaha Motor’s Casting Journey Our roots in casting technology lie in the techniques used to cast piano frames at Nippon Gakki Co., Ltd. (today’s Yamaha Corporation). Those techniques were adapted and applied toward creating the engine and parts for the first Yamaha motorcycle in 1955, the YA-1. Since then, Yamaha has continued to cast a plethora of parts not only for motorcycle engines but also for chassis, marine products, car engines, and more—all in-house. The capability to cast both large and small parts and components in-house has made us a rarity among the world’s motorcycle manufacturers. ![]() Producing the wheels for our motorcycles is a good example of this capability. In addition to vacuum die-casting aluminum wheels, Yamaha succeeded in casting magnesium wheels for mass production with the YZF-R1 in 2015, something once thought unfeasible for a high-volume product. The flow forming process for creating Yamaha SpinForged Wheels was also already often employed when producing wheels for cars, but motorcycle wheels require an appealing design on both sides, thus adapting flow forming for our industry presented high hurdles. To clear them, Yamaha carefully selected an aluminum variant to work with, conducted repeated experimentation of different alloy combinations in search of the right strength and lasting toughness, and devised the ideal heat treatment method to match. The Yamaha SpinForged Wheel was the result of this work and more. |
Message from the Editor I want to share some of the other things Oshima-san said as we spoke with her. “I think materials and materials research don’t particularly grab the spotlight compared to design, engineering, and the like, but I personally like being in that ‘unsung hero’ role,” she admits with a smile. She holds a firm belief that if we make advances in the materials we have available, then that will serve as a catalyst for technological progress and innovation. “That’s why it’s fun to examine and experiment with materials,” remarks Oshima. “It may not be flashy but it’s good, worthwhile work.” Maiko Kawai |